Meeting Recap: The Secrets of Horological Engine-Turning (Guilloché)
Video recordings of lectures are available to members immediately (using your membership password), and the general public with a 2 month delay.
Joshua Shapiro, Watchmaker and Owner of J.N. Shapiro Watches
February 4, 2019
At the February 4, 2019 lecture at the Horological Society of New York, Joshua Shapiro, Watchmaker and Owner of J.N. Shapiro Watches, graced attendees with his passion of engine turning and how growing up in a machine shop steered him towards watchmaking. Shapiro divided his lecture, The Secrets of Horological Engine-Turning (Guilloché), into four parts:
What is engine turning?
How does engine turning work?
What is the history of engine turning?
What is my contribution?
WHAT IS ENGINE TURNING?
Shapiro made sure to point out that ‘engine turned’ is spoken in English-speaking countries, whereas ‘guilloché’ is used everywhere else. The three machines that Shapiro highlighted were the Rose Engine Machine, Straight Line Machine and Brocading Machine.
HOW DOES ENGINE TURNING WORK?
Rose Engine Machine: The most famous and recognized, the machine is used for circular lines as the transfer workpiece is stationary then locks. Images of the MADE Rose Engine Machine used by David Lindow and the Frank Dorian 1851 Custom Made exemplified the workings of rose engine machinery. A video of the rose engine showed an example of a hand-operated machine creating a heart-shaped rosette. The magnification (10x) of the pattern was to check that if the cutter is dull, the engine turning will be dull.
Straight Line Machine: Though not as aesthetically pleasing as the rose engine, the straight line machine produces vertical line engraving. The bars are traced and the bar is moved to change the pattern. A video of the straight line machine showed a microscopic view (30x magnification) of the diamond pattern. Not only is the diamond a common pattern, it is also the easiest engine turning pattern to make. Straight line engine turning, however, calls for a border. The border patterns cover up the end marks - so when you are looking at a watch, see how the marks are covered up in straight line machining.
Brocading Machine: Also known as ‘medallion machine’, this is unlike the rose engine or straight line machines because an active operator is not required. The automatic version of the machine produces a pattern that is utilized by Audemars Piguet for their Royal Oak dials.
WHAT IS THE HISTORY OF ENGINE TURNING?
The rose engine was invented in the early 1500s and was more complex compared to the bow/pole lathes. The first engine turned watch was made around 1680 in a wave rose pattern. Also, keep in mind that the ornamentation was for royalty and the rich. Shapiro also pointed out the people who were key in engine turning history: Jean-Antoine Lépine, Pierre Benjamin Tavernier and Abraham-Louis Breguet.
Jean-Antoine Lépine: French watchmaker (1720 - 1814) who created thin pocket watch movements. It is thought that Lépine influenced Breguet since A.L. Breguet may have apprenticed with Lépine. Although ‘Breguet hands’ are attributed to its namesake, Lépine actually invented the design.
Pierre Benjamin Tavernier: Paris had skilled artisans that had the dual talent of case making and engine turning. Tavernier’s skill can be found on works for Lépine and Breguet.
Abraham-Louis Breguet: There’s no denying the aesthetic influence Breguet has on numerous brands such as Patek Philippe. His earlier dials were originally enamel and the movements were considered works of art due to their complexity and skill of Breguet frosting (a.k.a. depletion gilding). Modern Breguet dials are now gold and plated in silver - before it was either gold or silver.
Early 1900s: The popularity of engine turning began to burst - the rose engine and straight line machines are mass produced along with higher precision and quality during the Industrial Revolution. Items such as napkin rings, lighters, boxes, cigar boxes, pens, frames, eggs and several types of jewelry were receiving the engine turned treatment.
The 30s, 40s and 50s: During these years, engine turning became popular on wristwatches. However, due to remarkably thin dials, there is the test of trying not to remove too much metal or else it goes through the dial.
The 60s: The advent of quartz nearly killed the presence of engine turning due to no passing on of skills and machines being difficult to find.
The 80s and 90s: Throughout these years, the revival of engine turning was slow. However, it was led by George Daniels in his book “Watchmaking”. Large Swiss watch companies began hoarding the machines - not for use - but for show. Derek Pratt, who has been compared to George Daniels, revitalized the Urban Jurgensen watch brand by using the technique. Other contemporary watch dial engine turners such as Roger Smith, Jochen Benzinger, Kari Voutilainen, David Lindow, Roland Murphy, Bernard Van Ormelingen, Calina Shevlin, Brittany Nicole Cox and nameless individuals at Metalem, Breguet, etc., are working to keep engine turning relevant and alive.
CNC and Stamping: Both processes aid in mass production. The use of CNC machines is necessary for serial production and is common amongst the large Swiss brands and some independent brands. You can get good results from the CNC depending on the operator, but the value diminishes. The use of stamping is used on a larger scale than CNC - however, since there’s no cutter, the sharpness is lost. Near the end of his lecture, Shapiro made a point to give a consumer warning, “Companies that make engine-turned dials are proud of it. Buyer beware if you can’t find any media of them making actual dials!”
WHAT IS MY CONTRIBUTION?
Shapiro strongly wants to contribute to the expansion of engine-turning and horology, particularly in the United States. After accomplishing the Basket Weave technique (which took six years to accomplish since it is one of the most difficult patterns to do) he started a brand new pattern termed Infinity Weave. The pattern is made by making small boxes that are done one line at a time. Shapiro wanted to push himself to the limit with the Infinity Weave because it is very easy to make a mistake and the process needs to be re-done. For the future, Shapiro wants to continue with the Infinity pattern on 40mm cases and experiment with other metals. Finally, there are plans to engine-turn on UWD movements and to create an American made movement within two to three years.
HSNY thanks Joshua Shapiro for his lecture!
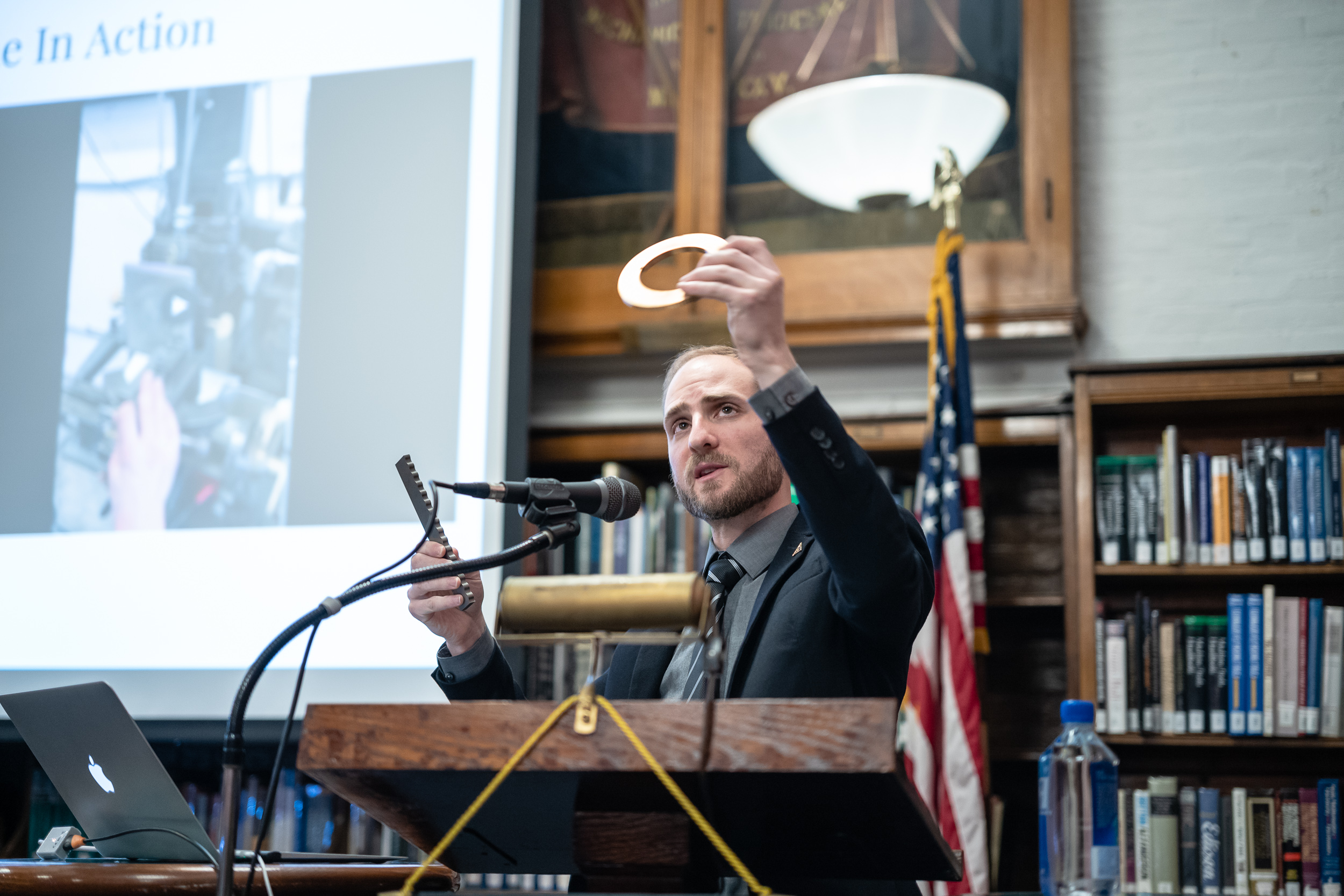
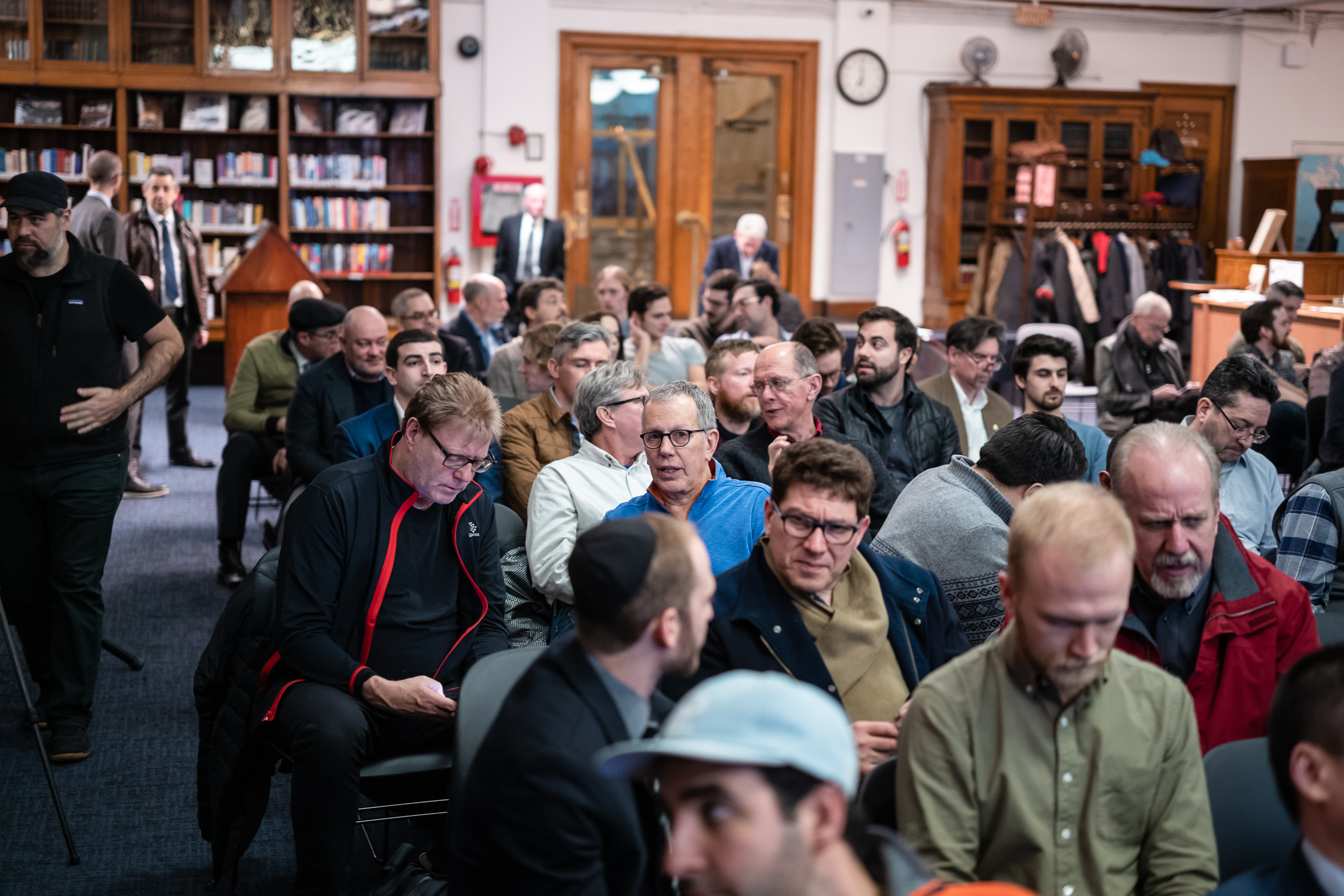

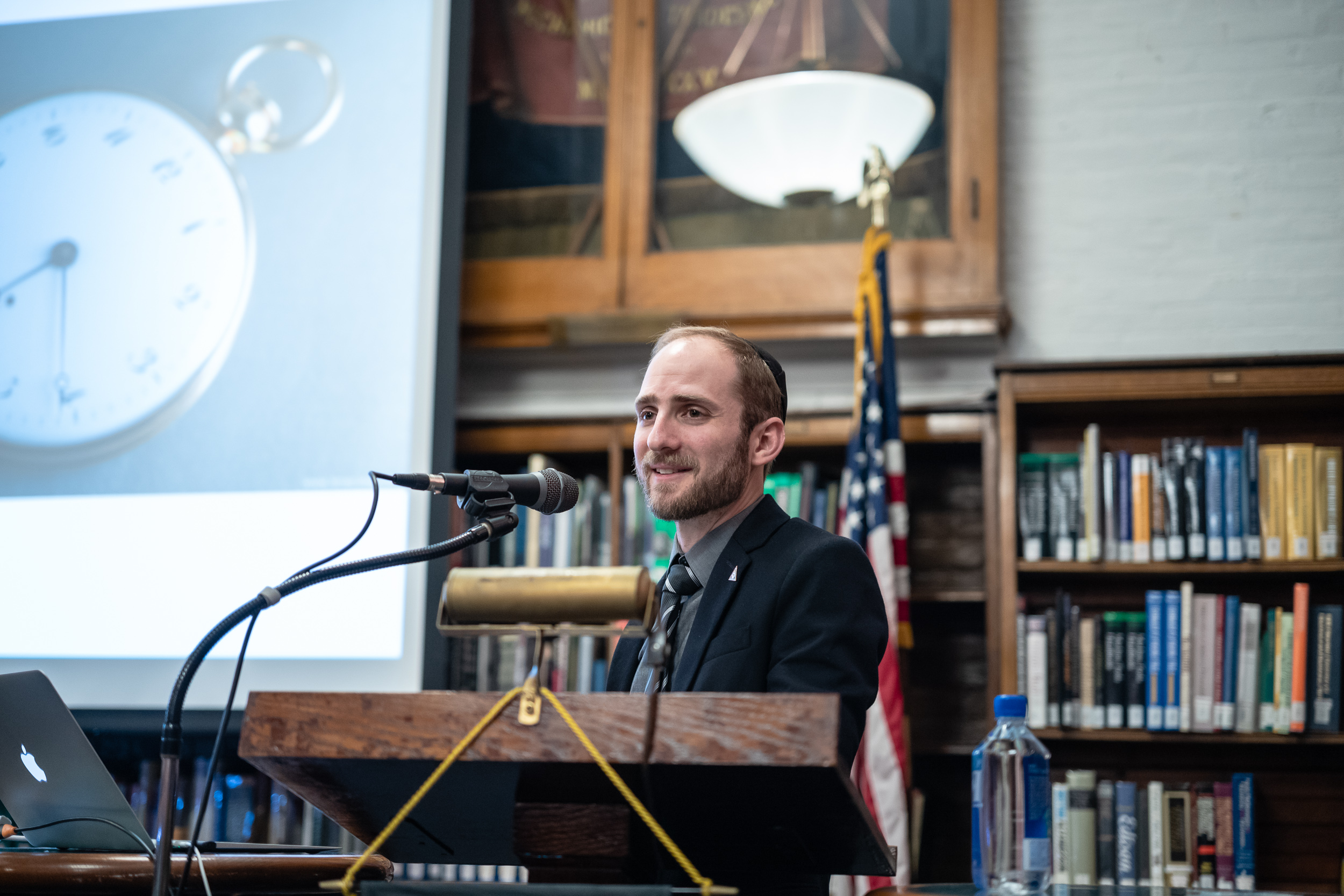
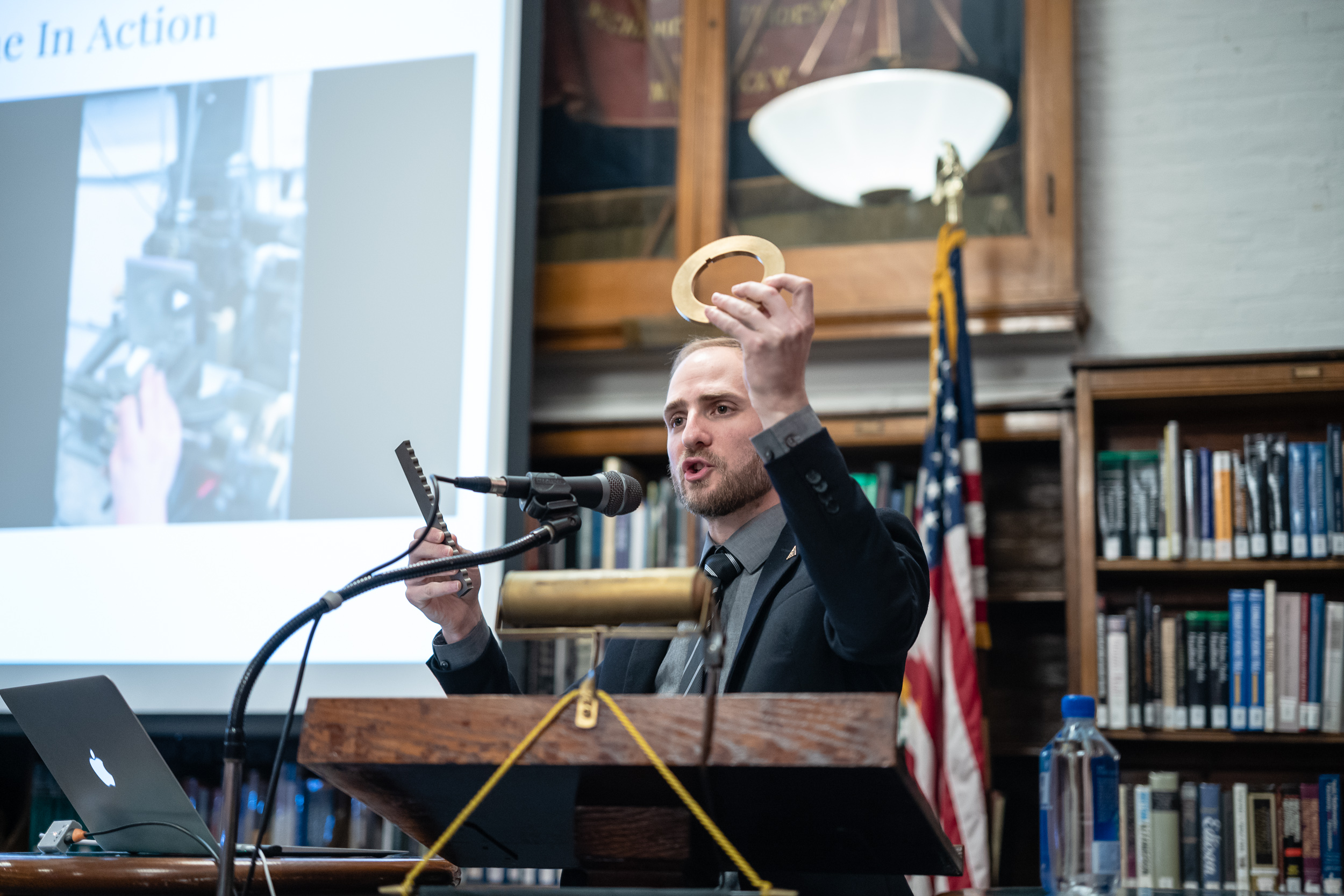
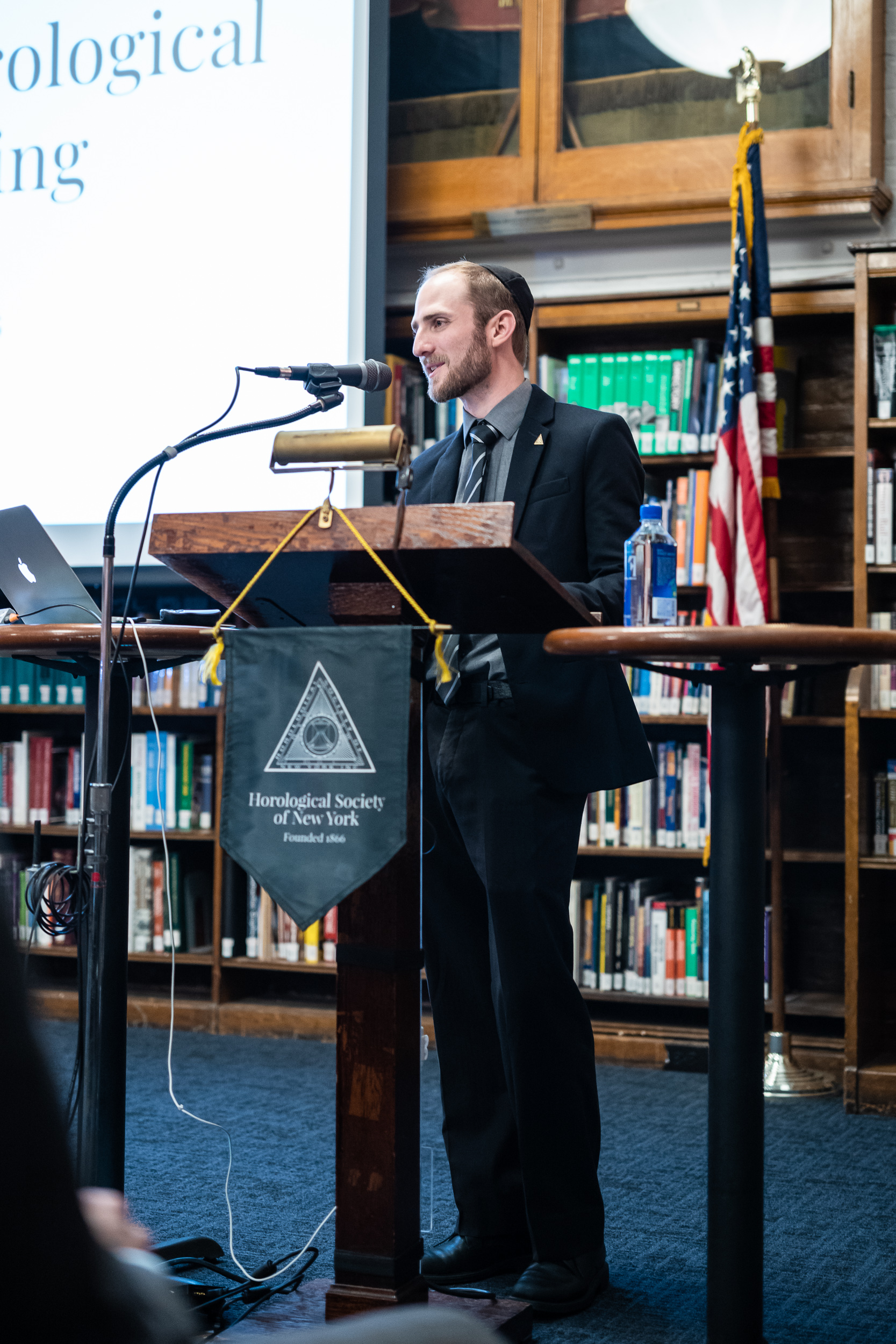

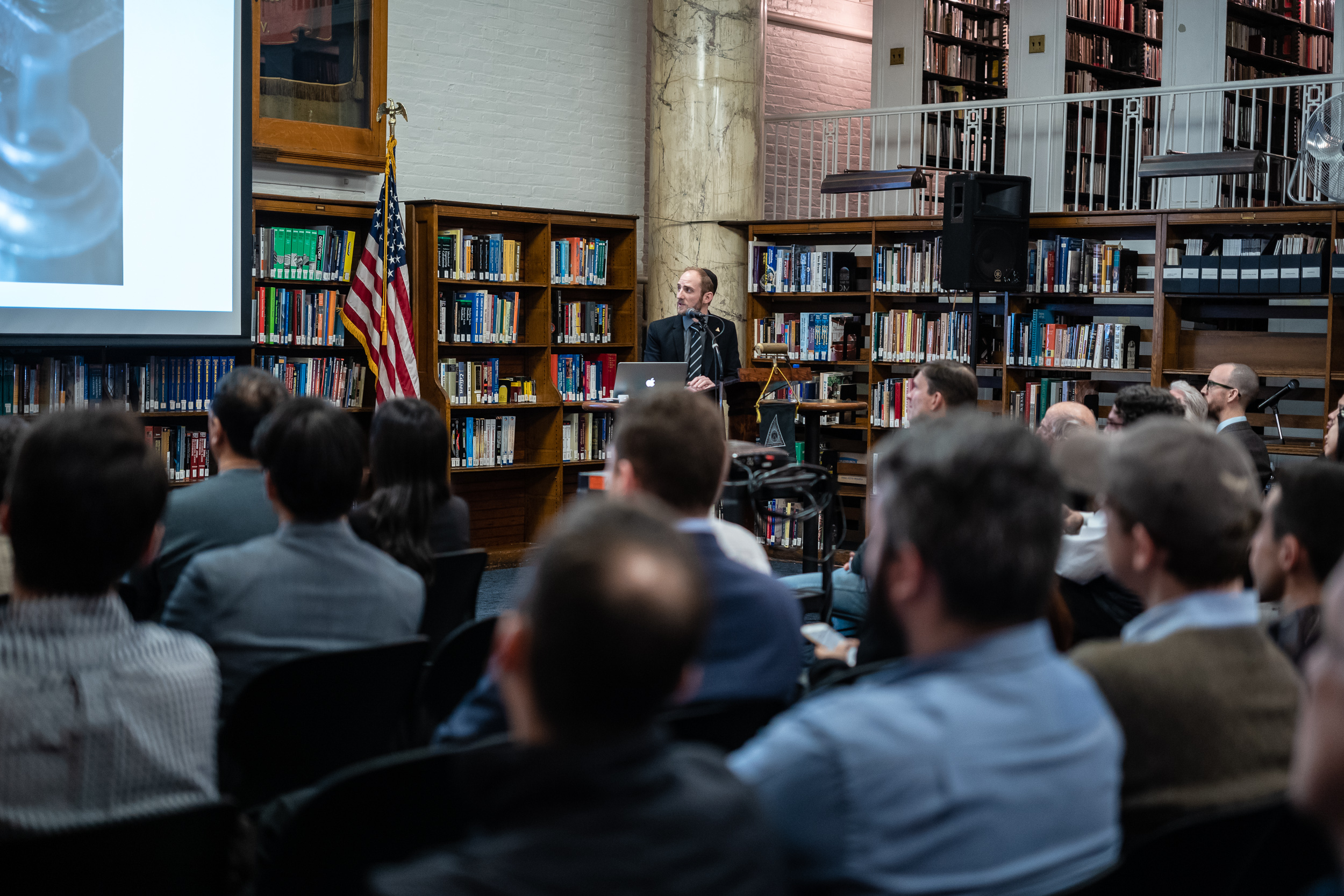
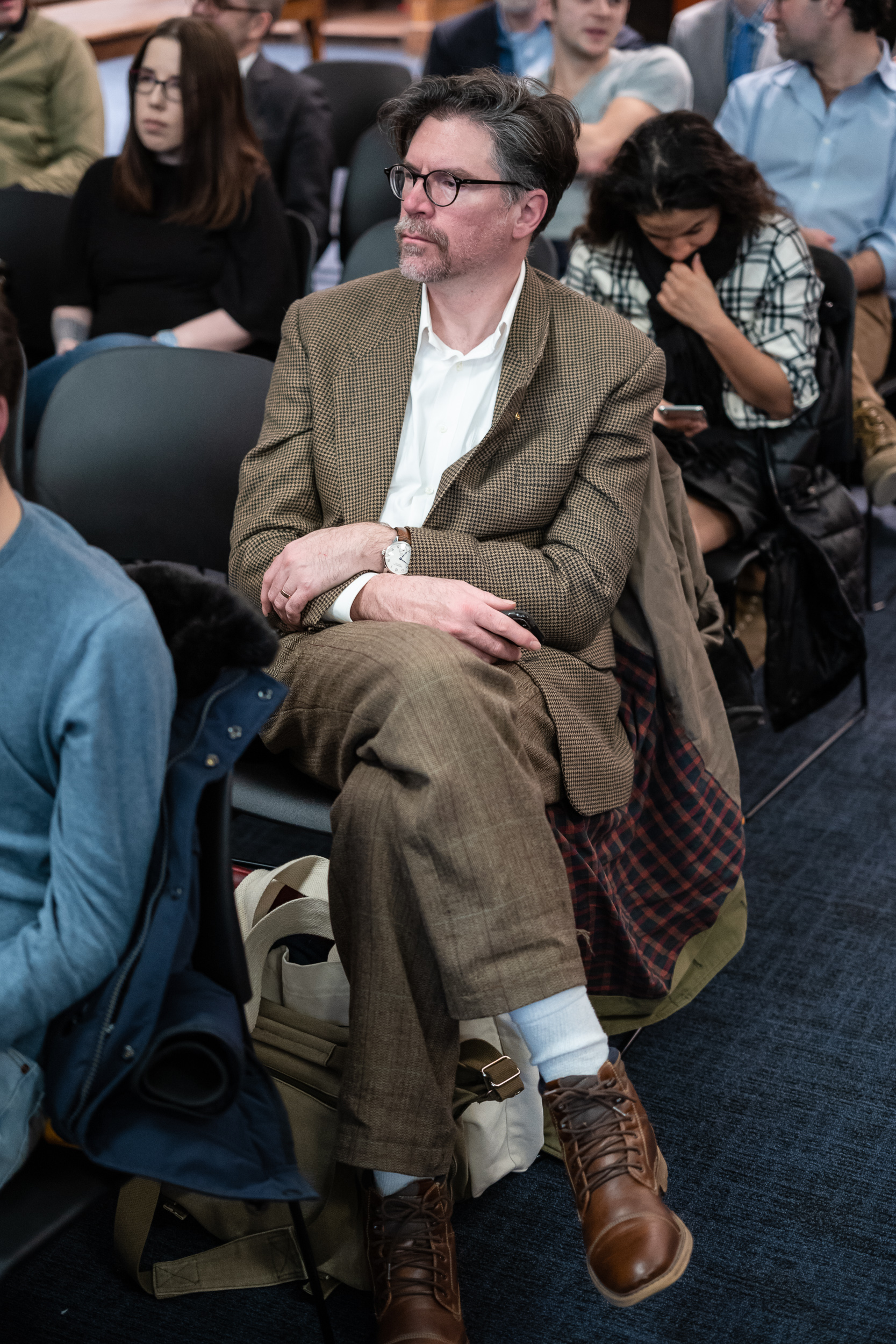
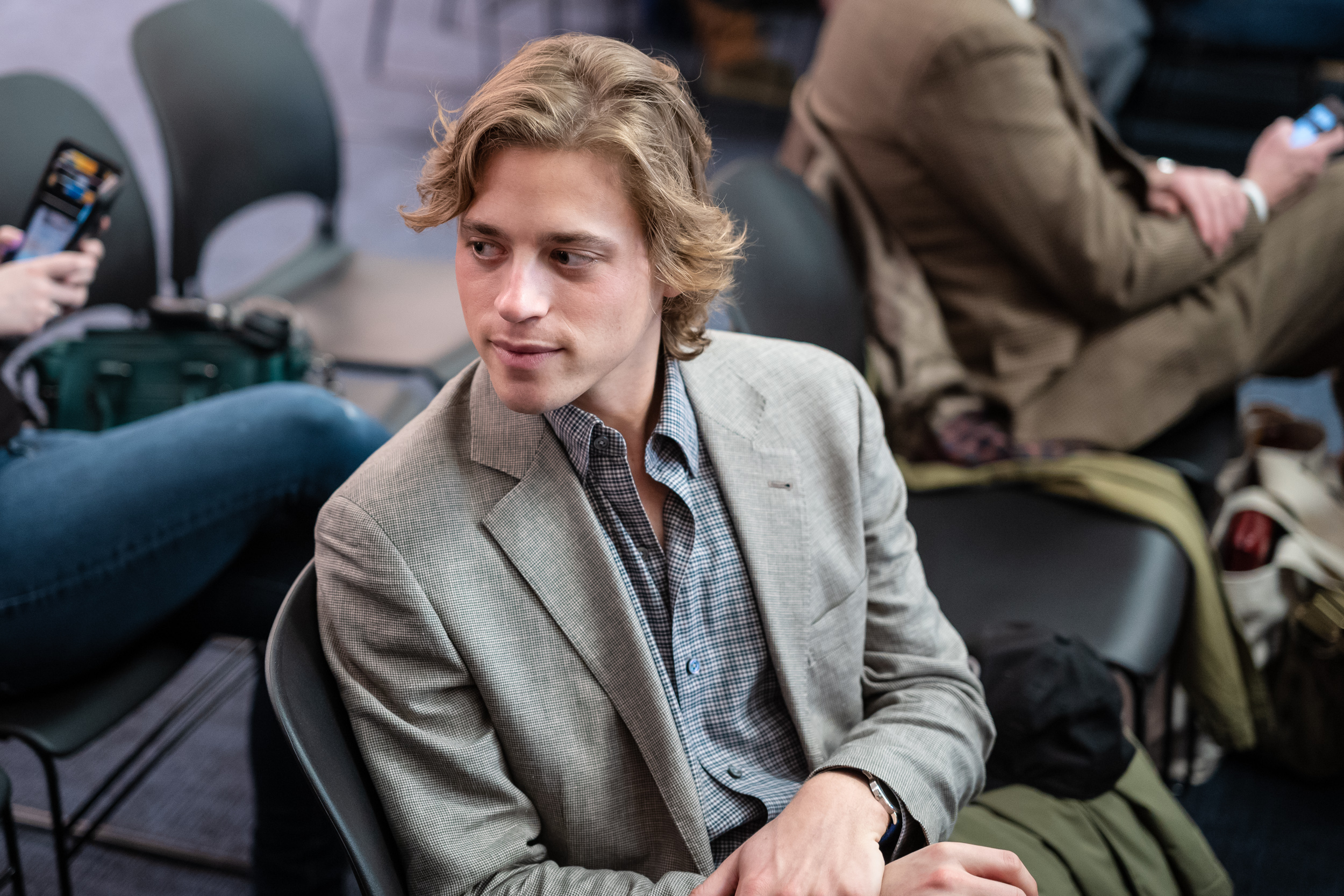
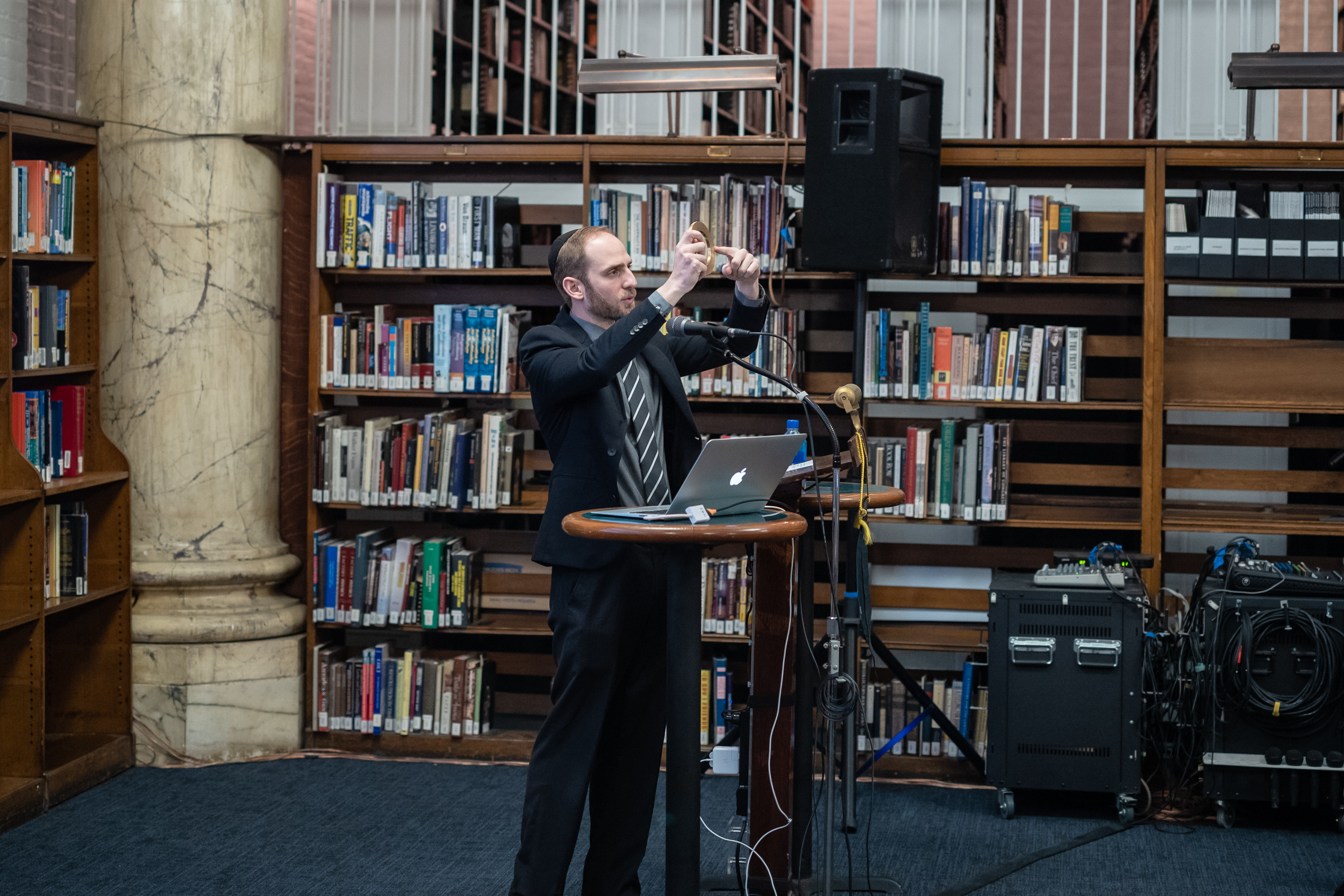
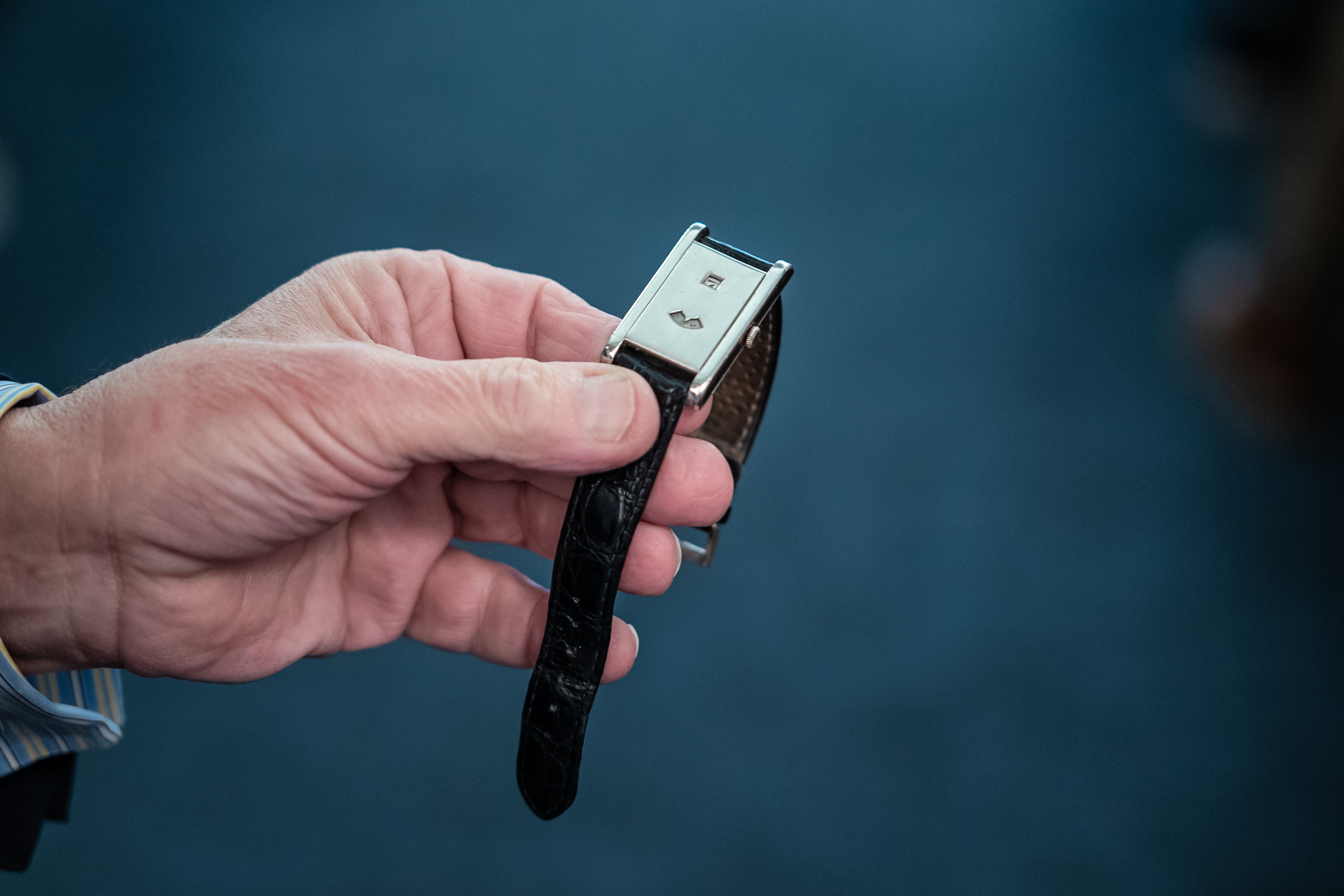
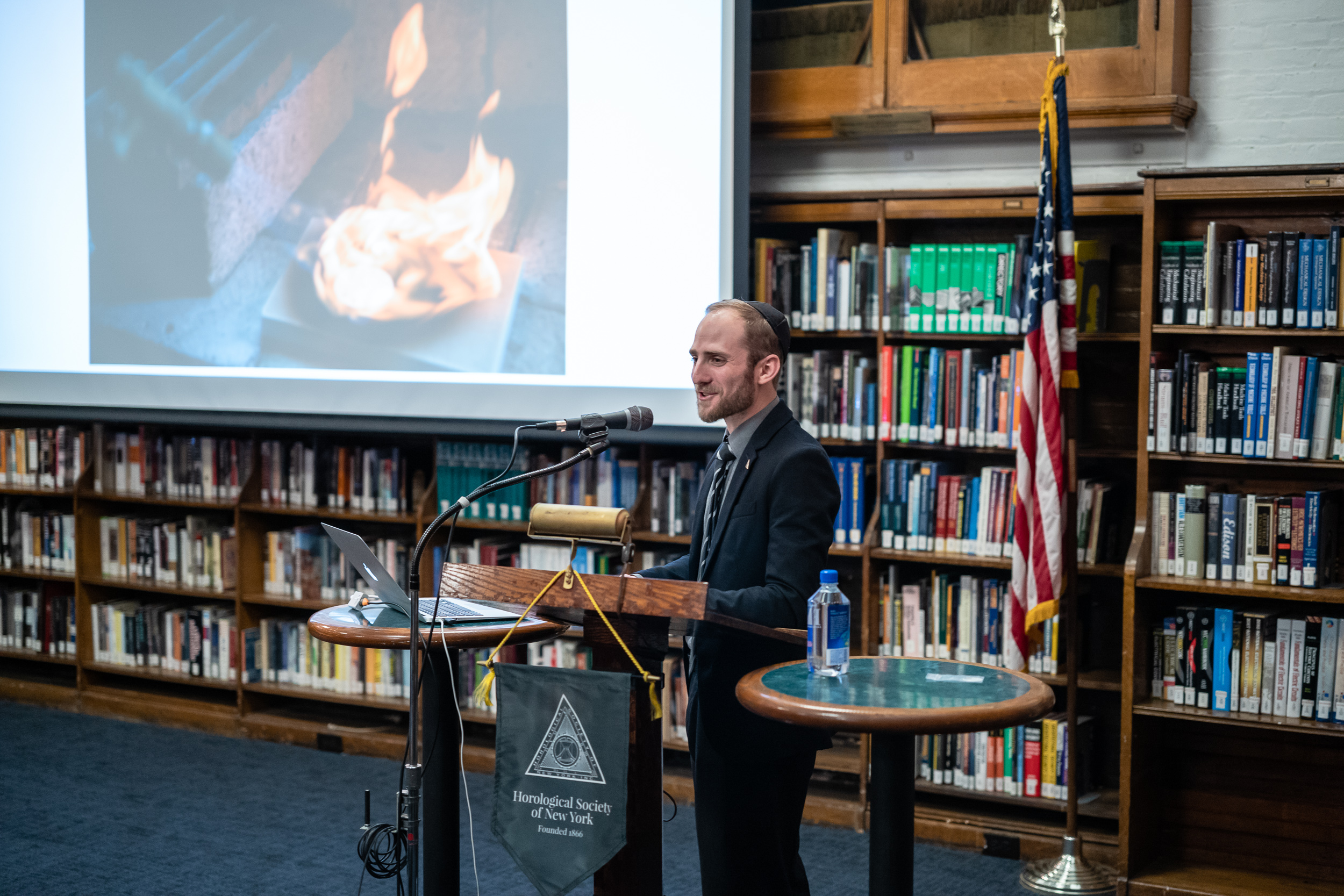
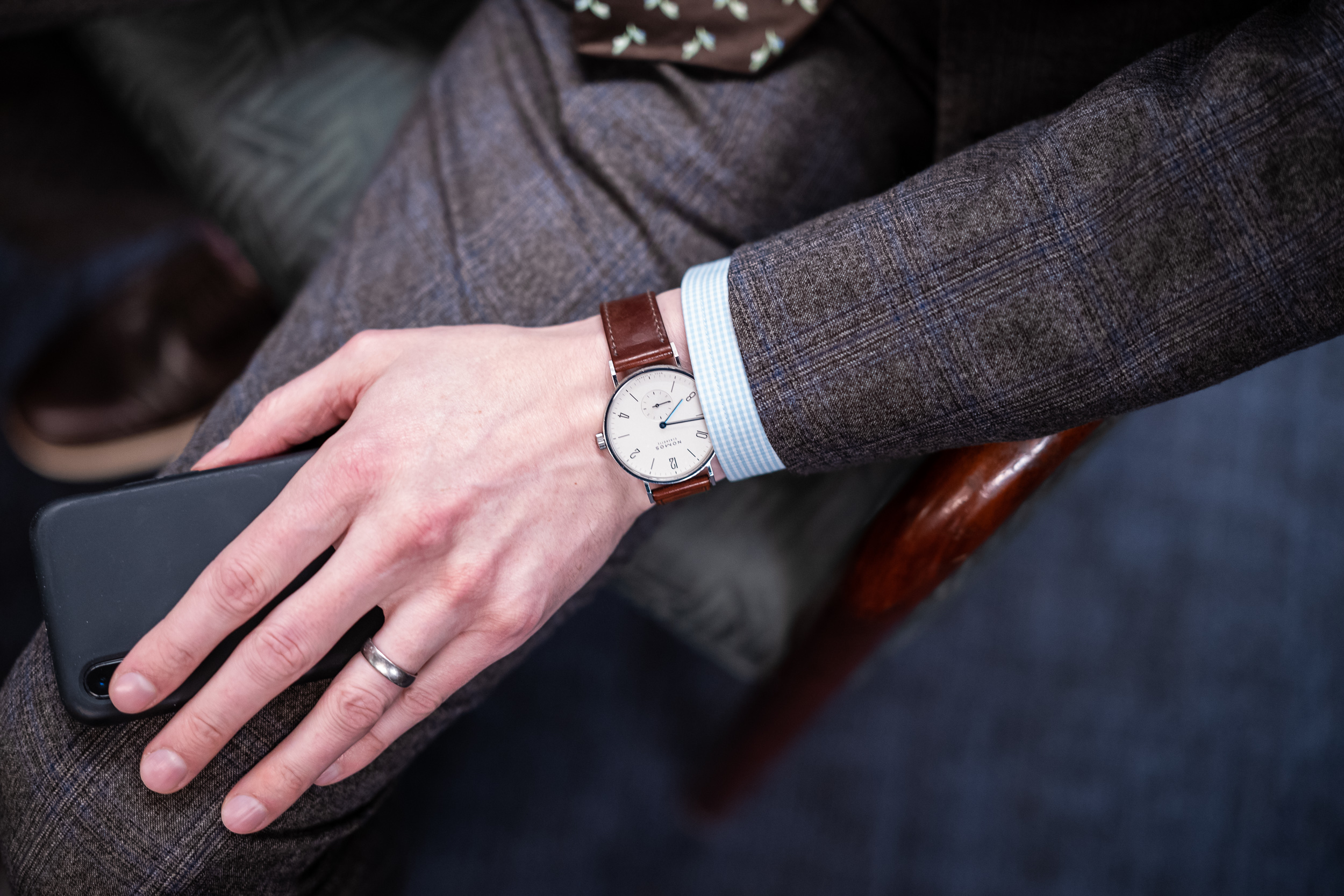
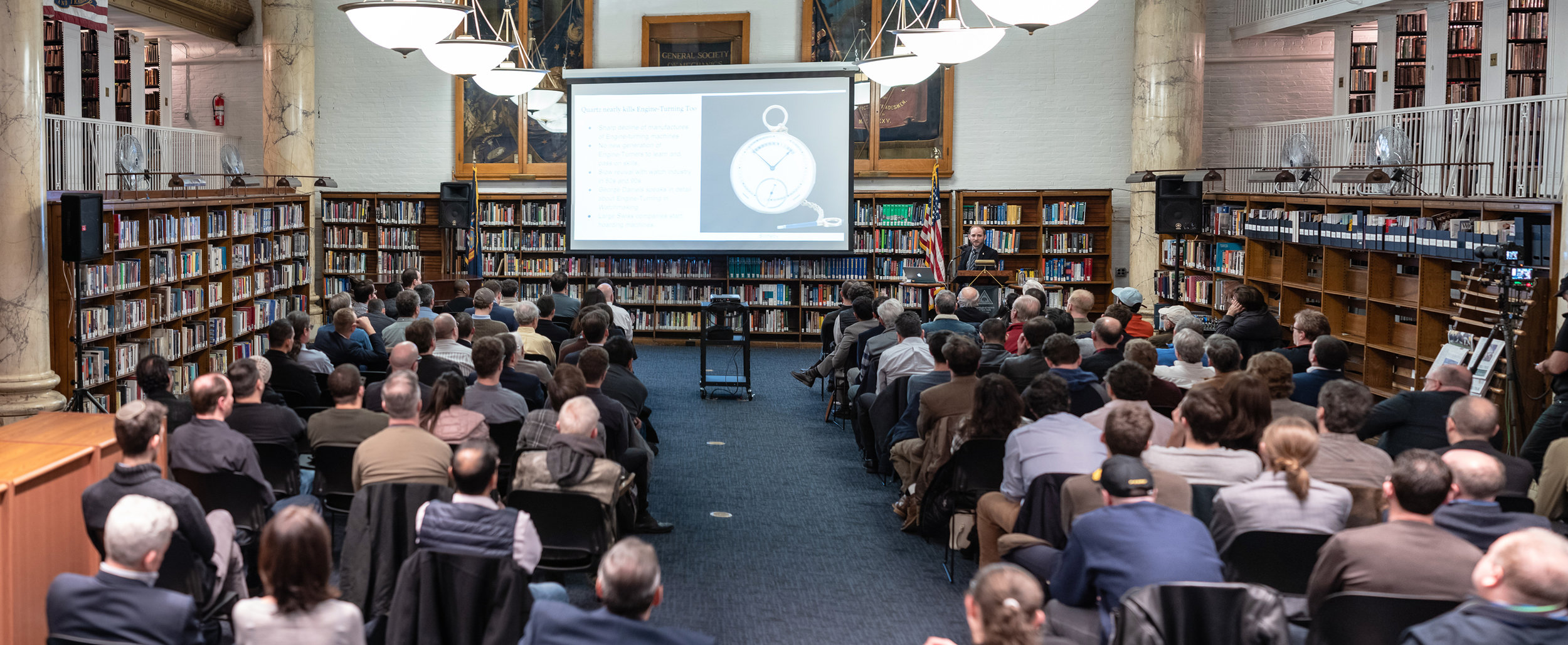
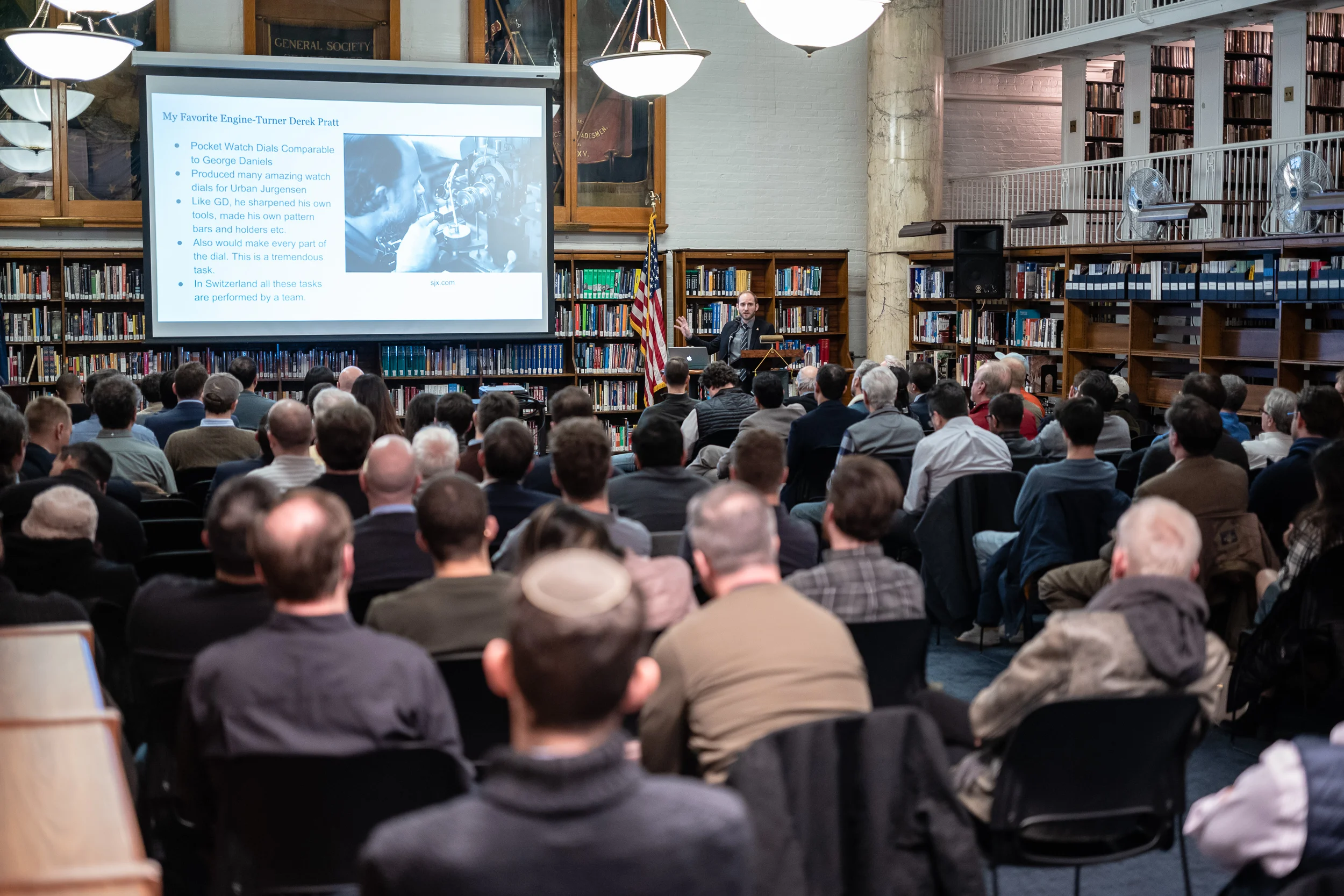
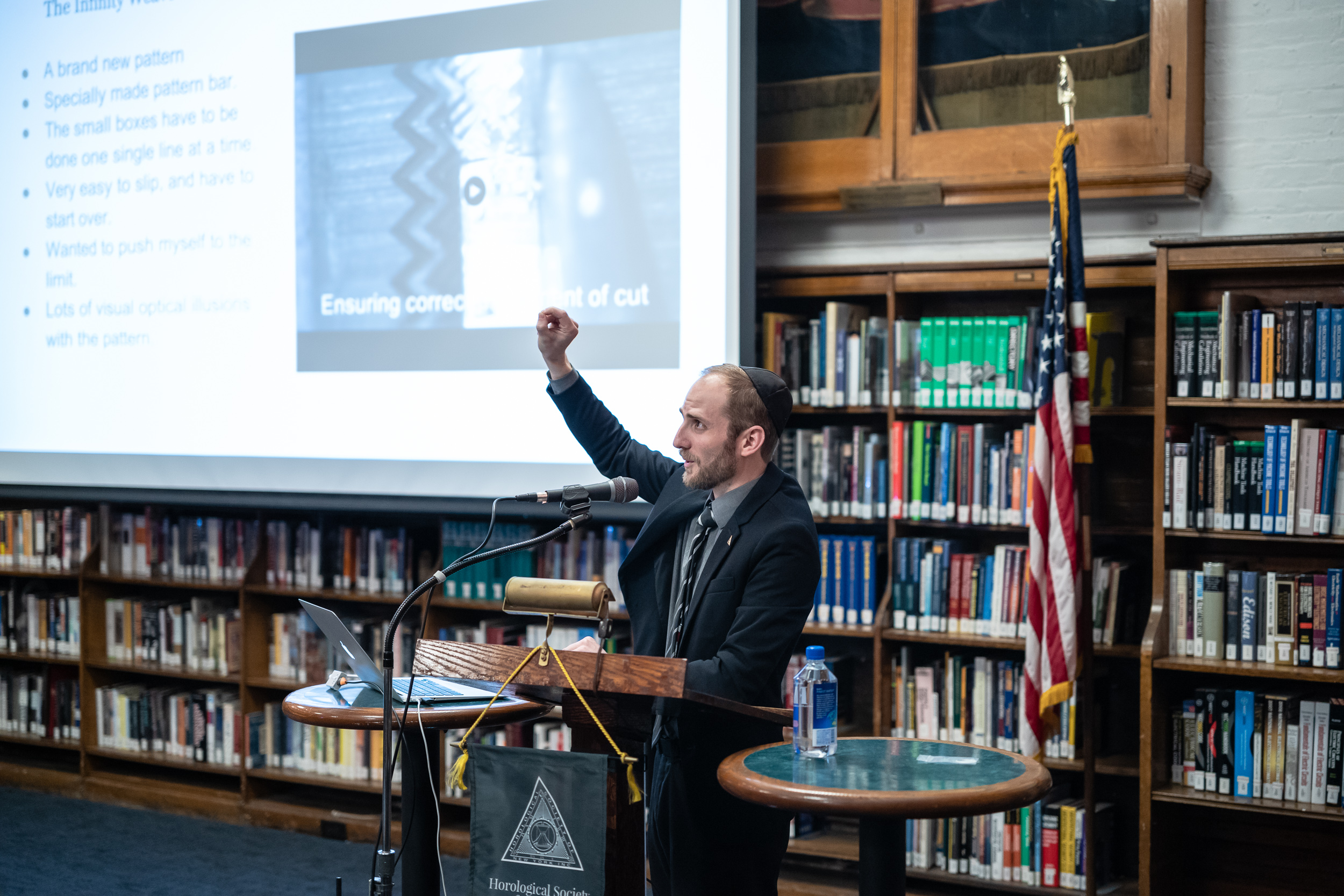
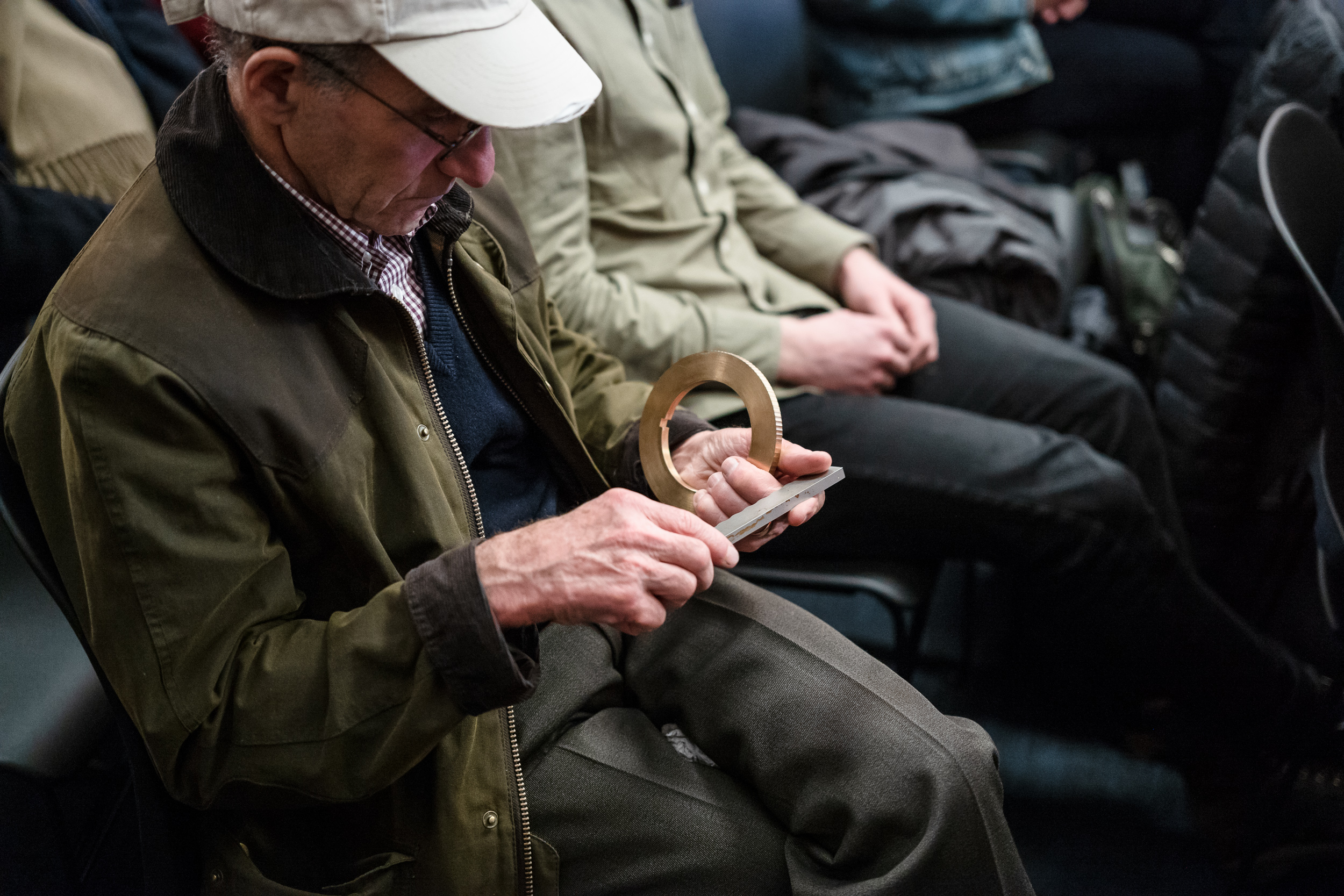
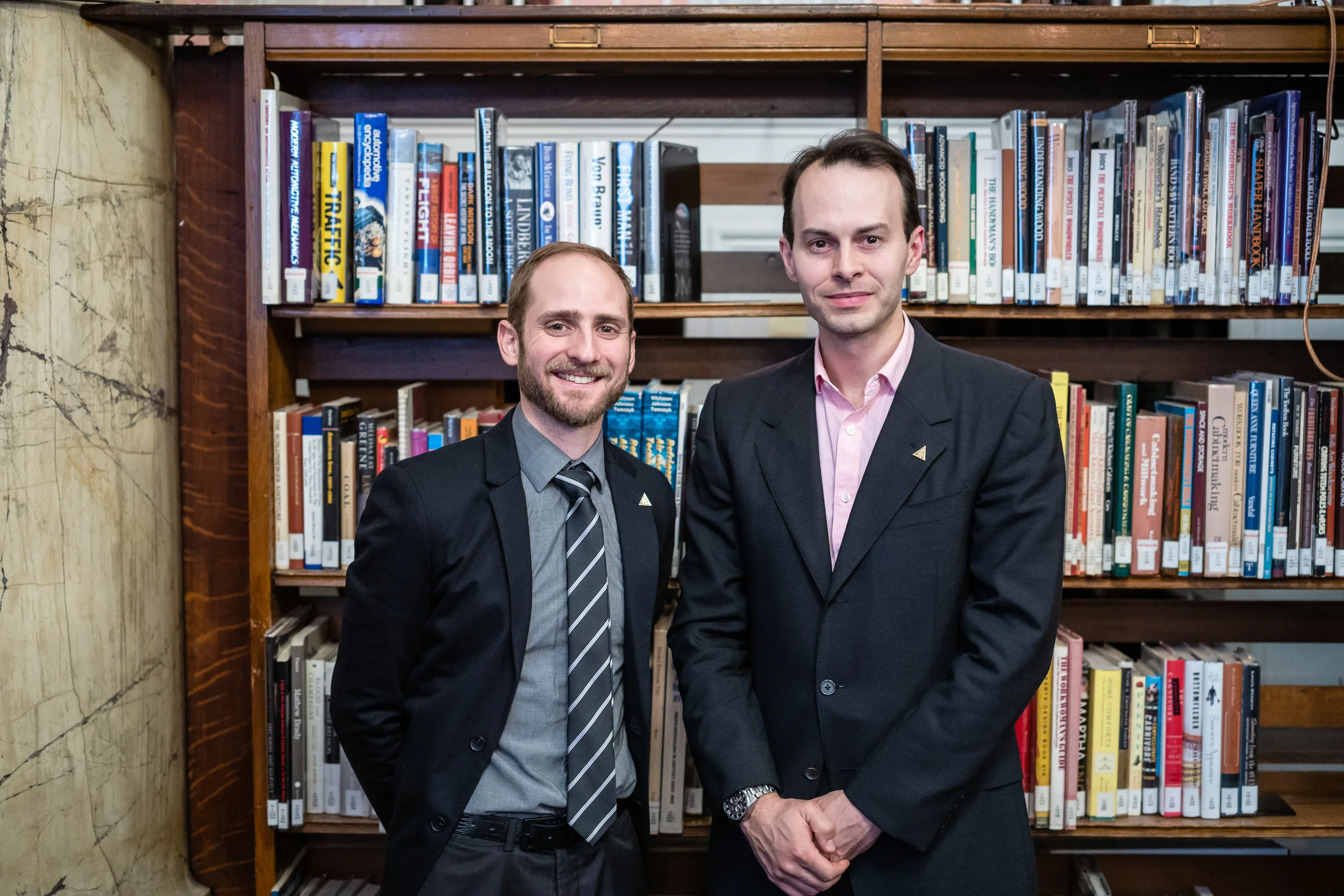
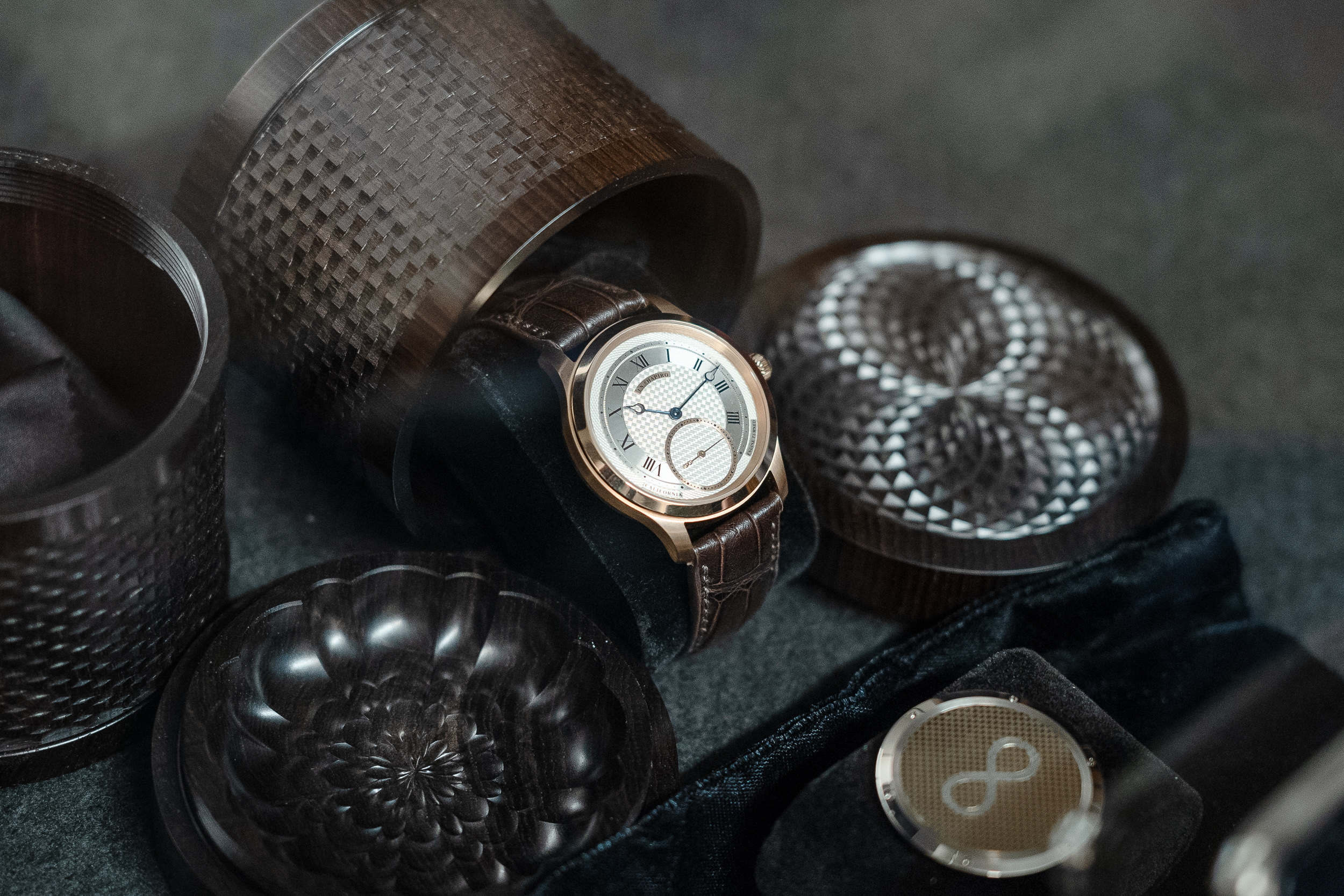
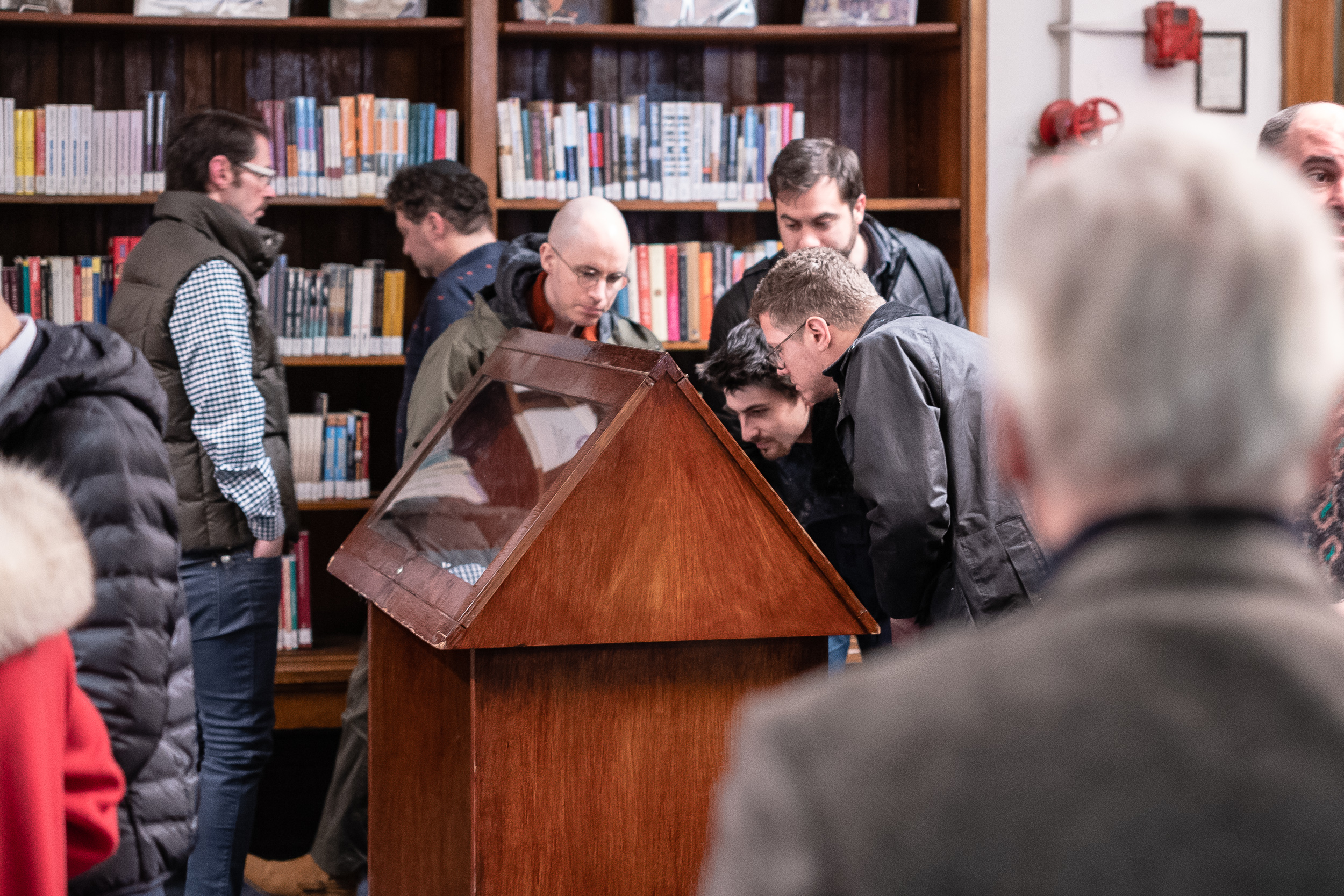
Photography by Atom Moore
Submitted by Melody Benloss, HSNY Librarian & Recording Secretary